The EPS industry shifts to low carbon energy sources
Brussels — Producing Expanded Polystyrene (EPS) is a task that requires a lot of energy. Smart Packaging Europe members have been doing their best to be smart about the energy they use to produce EPS. Over the last few years, the industry has taken drastic measures to ensure that energy used is as climate friendly as possible.
Since the early 2000s, many EPS producers have invested in expensive systems that make their plants better for the environment. Many of such systems are key for the efficient and more climate friendly production of EPS in Europe.
The installation of solar systems in plants and recycling facilities throughout the continent is one of the most efficient methods to boost the availability of green energy by the industry. In Austria, for instance, the HIRSCH Servo Group has been able to undergo a continuous reduction of its ecological footprint through large-scale investments into photovoltaic systems as well as energy-saving lighting, heat recovery, and energy monitoring. The new 6,350 m² photovoltaic system on the roofs of the HIRSCH Servo Group’s Glanegg site, with an approximate output of 1 GWh of renewable electricity annually, has been particularly key for its green transition. Via the Kelag grid, HIRSCH Servo Group’s surplus electricity also reaches private households, which are supplied with renewable energy.
Another Smart Packaging Europe member, Aeropack developed an energy efficiency programme with a similar solar system in its facility in Grünstadt, Germany. This programme started more than a decade ago, and ever since has been upgraded many times. One of its upgrades was the provision of the latest energy supply in the field of steam generation as well as the allocation of the latest air and vacuum technology to improve its efficiency. All such efforts allow for a more sustainable production of EPS.
Yet some EPS producers have gone even further. Some have invested and created new companies to develop and implement zero-emission technologies and electricity production from renewable sources for themselves. One of them is the Synthos Group in Poland.
Apart from having its photovoltaic farm, the Synthos Group has also founded Synthos Green Energy. A highly innovative company, this firm currently focuses on two projects: offshore wind farms and small reactor nuclear power. They already submitted four applications to the Polish Minister of Maritime Economy for a permit to start offshore projects. If approved, the offshore wind farms would have a total output capacity of 1260 MW for all the Group’s facilities. In terms of nuclear energy, the company has become a strategic partner of GE Hitachi in BWRX-300 technology development, a Small Modular Reactor (SMR).
Yet, sustainable production begins long before turning raw materials into EPS with green energy. The equipment at EPS locations plays a major role when it comes to protecting resources. Many Smart Packaging Europe members are deeply committed to efficient energy management and continuously optimize the energy footprint with a variety of modernization measures.
Our member Storopack, for example, saves 850 metric tons of CO2 a year in their Krumbach location thanks to more efficient energy management and a wide variety of modernization measures. Another modernisation by Storopack has been the installation of new LED lamps at many locations. As a result, Storopack is saving 45,991 kilowatt-hours a month. These are little steps compared to Synthos wind farm projects, yet every little step that companies can take forward to protect the environment is valuable.
All the above examples are clear demonstrations of the willingness of the EPS industry to adapt to a more climate-friendly world. From Synthos offshore wind farms and nuclear reactors to the simple yet efficient modernisation measures by Storopack, every step puts the industry closer to achieving its environmental targets. Going forwards we will see many others joining the ones above and shift to low carbon energy sources.
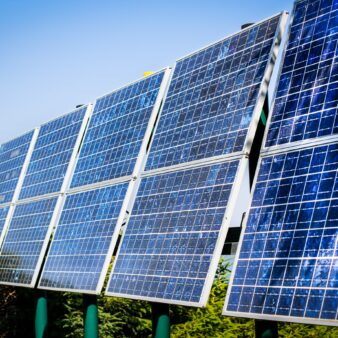